Sintering parts manufacturing
Can I use sintering for my parts ?
There are several limitation to the use of the sintering process for your metal parts :
- Size limitations, we can provide parts that fits into the range of D10mm to D220mm only.
- Quantities : the MOQ for sintering production batch is between 500 and 1000 parts according to part size. Usual order size are closer to 10 000 parts.
- Due to the process the shape of the parts are limited or will require additional machining and thus will be more expensive.
- Material quality, while the strength of the part is very good, forging should be preferred for very critical parts.
Sintering references :
Why using sintering ?
AGCIS explains below what are the advantages of sintering :
Easier for some complex shapes :
For gear wheels sintering allows a quick manufacturing without additional machining. Vertical holes can also be directly made out in the mold.
High precision:
Manufacturing tolerances are different in height and width. In width, basic tolerances are IT 8-9 (equivalent 0.08 to 0.09mm for 10mm dimension), and can reach IT 5-7 (0.05 to 0.07mm for 10mm) if a calibration (see below) is made.
For the height of the part, tolerances are IT 10-13, which is equivalent to 0.1 to 0.13 mm for a 10mm dimension.
High repeatability:
The sintering process use mold and high pressure, this ensures high repeatability of the parts and therefore a stable quality.
Large possibilities of materials:
Metal powder can be custom mixed with most of the elements, that enables an infinite possibilities of materials characteristics.
Lighter parts:
Due to the microstructure of the sintered parts that include micro-porosities, parts are lighter than equivalent casting or machining parts.
Surface rougthness:
Parts made by sintering have a generic good surface rougthness, that can be improved by surface treatment at the end of the production process.
How a sintering factory works ?
Detailed process of a sintering factory :
First the material is blend to obtain an homogeneous mix of metal powder.
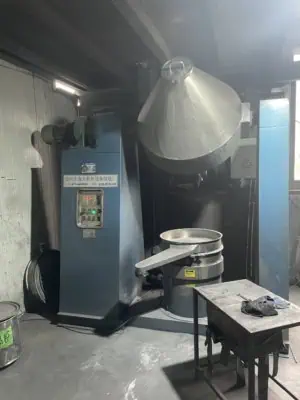
Metal powder blending
Then that powder is heated and pressed into a mold at several hundred tons.
Sintering press
The next phase is removing the oil into a first in-line automatic oven.
Oil removing by heating
Then the parts are entered in the sintering mold, which will heat the parts just below their fusion point.
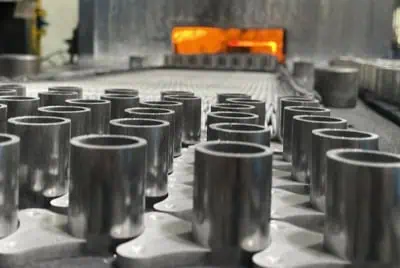
Sintering oven
If tight tolerances are required, the parts are pressed a second time in a calibration mold.
Calibration press
Finally the parts will be cooled and may receive additional post treatments like heat treatment, sanding or painting.